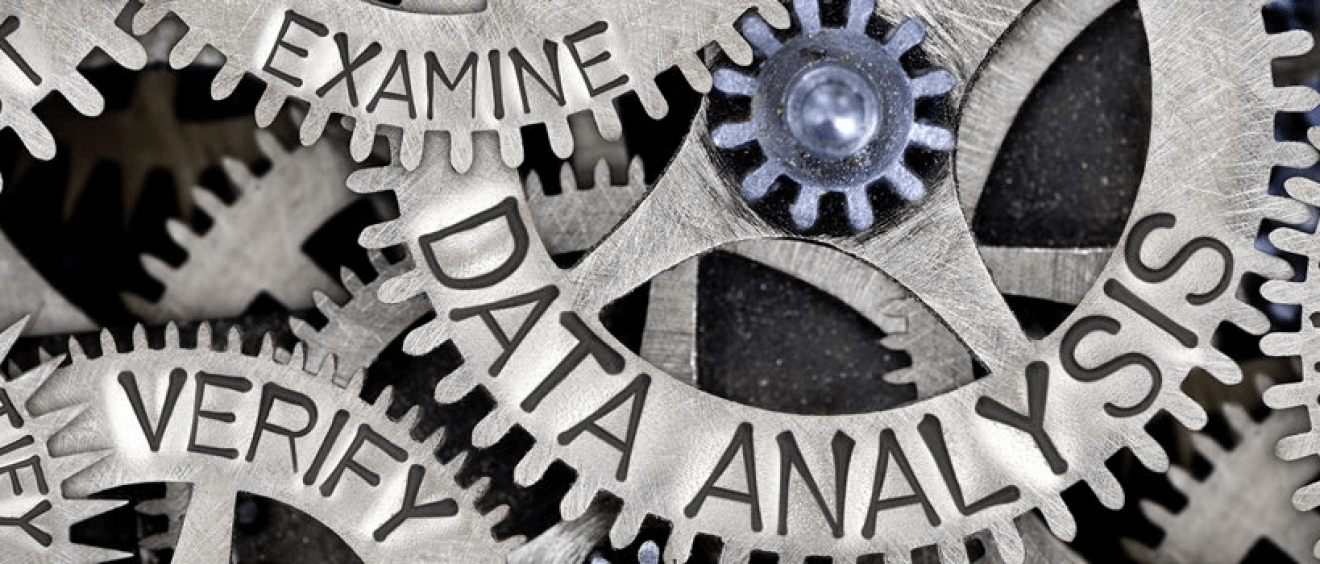
New Solder, Same Old Testing
Solder is in arguably one of the required building blocks for electronic assemblies, and every assembly in the world has it.
Solder, has been around for over 5,000 years, by some accounts, and used for weapons, jewelry, and stained glass, among other items.
In 2006, everything changed for the vast majority of contract manufacturers with the RoHS directive that effectively removed lead from the soldering process for all products to be built or imported into the EU
Removing lead increased the amount of thermal energy required to melt the solder and create a good MIC. Removing lead also increased the risk of tin whisker formation.
Based NASA assertion Since removing lead promotes tin whiskers, it was necessary to add other metals to help mitigate whisker growth, and the most popular solder on the market is SAC305 (tin/ silver/copper).
A lot of research is being done to formulate a better solder regarding solder joint strength and tin whisker mitigation as part of ongoing advances in soldering.
Other paste formulations are adding bismuth or zinc for lowering melting points, but those additions come with the trade-off of more risk for oxidation.
One of the biggest advancements we have seen around here is jet-printable solder paste. This is certainly not a new technology, but as of today, we have not seen widespread adoption of jet printing, so we would consider it fairly new.
There are already a few companies using this technology, and from a reliability standpoint, we see the biggest benefit in the way it reduces bridging and/or skips from dirty stencils and excessive solder applications, which reduces the amount of flux applied.
the best place to start will usually be IPC for guidance on how to best determine which test is applicable to your product. The basic visual inspection and acceptance criteria are found in the IPC-A-610 standard that covers all types of solder joints.
Cross-section is the best tool available for determining solder joint quality. it is really the only way to see if your assembly process is forming a solder joint that is acceptable. Cross-section with SEM (scanning electron microscope) inspection is also a crucial step in qualifying any soldering process because you need to get in there and see how well the solder is wetting to the pad and look for cracks and voids and any number of other conditions that weaken the joint. This is on top of the vibration testing and thermal cycle/ shock test to determine the fatigue effect on the joint. Without that proof, you have nothing but unanswered questions about reliability.
If no failures are indicated by the dye, then other test methods such as cross-sectioning, acoustic microscopy, and EDX or SEM analysis may be the next steps in finding a root cause in the BGA solder joint failure analysis.
Article New Solder, Same Old Testing By Eric Camden, FORESITE INC