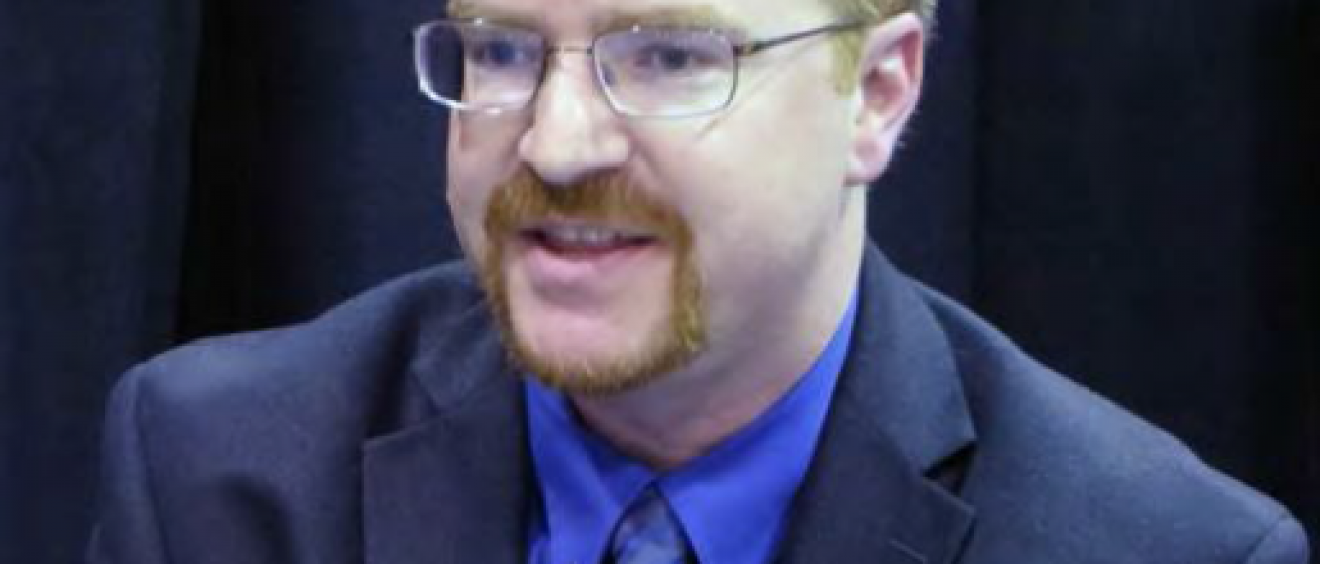
Electronics Cleanliness Testing – Part 1
whitepaper : Electronics Cleanliness Testing
Abstract
This study is an investigation and comparison of the performance of no-clean liquid wave soldering fluxes using a commercially available localized extraction and cleanliness testing system and surface insulation resistance (SIR) testing.
The flux test coupons for both tests were prepared in accordance with IPC TM-650 2.6.3.3. The IPC B-24 coupons used were manufactured using a lead-free wave solder process. Coupons were then tested for SIR per J-STD-004B using IPC TM-650 2.6.3.7 and tested with localized cleanliness testing.
The results for 15 no-clean fluxes are presented: three VOC-free rosin-free fluxes, two alcohol-based rosin-free fluxes, and 10 alcoholbased fluxes with rosin. The results with six of these fluxes were demonstrated in Part 1 of this study.[1]
A divergence in test results is observed between the J-STD-004B SIR pass/fail requirement of 100 MΩ minimum and the clean/dirty results provided by the cleanliness test system. The SIR resistance/time graphs and cleanliness tester current/time graphs are compared. The Corrosivity Index (CI) calculated based on the result of localized cleanliness testing is compared with final SIR values for the fluxes.
Introduction
Surface Insulation Resistance Tests
There are various test methods available for assessing SIR properties of no-clean flux residues, including those published by IPC, Bellcore, and Japanese Industrial Standards organizations. All SIR tests are accelerated electrochemical reliability prediction tests for no-clean fluxes that incorporate manufacturing conditions and service environment factors in the test methods. Although specific conditions can vary across the test methods, each test incorporates the following characteristics:
1. Test coupons utilizing comb patterns with defined comb width and spacing
2. Sufficient flux loading applied to each comb pattern
3. Coupons are processed in a wave solder system in both comb up (preheat without solder wave contact on the combs) and comb down (preheat and solder wave contact) orientations
4. Applied bias and exposure to accelerating fixed temperature and humidity environments
5. Quantified pass/fail minimum resistance criteria
6. Qualitative pass/fail inspection requirements after environmental conditioning
continues…